Flex Assembly Tips :
Array Options:
There are many ways to panelize a flex circuit for assembly. For your array design keep in mind the following:
- Tab routing is the best way for flex, instead of scoring
- Use local fiducials within the flex circuit
- Use lots of copper for stability
- Optimal sizes depending on the size of the flex and component feature. We recommend: 5 x 5”, 5 x 10”, 8 x 10”, 10 x 10”, 10 x 16”
- Methods of singulation of parts: Xacto knife, Laser cutting, Die-Punch, Routing
- Singulation process should not induce stress in the solder joints
Here are some different array examples:
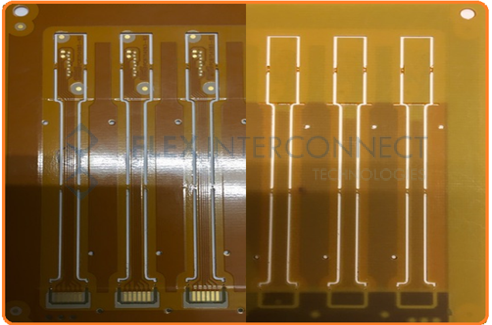
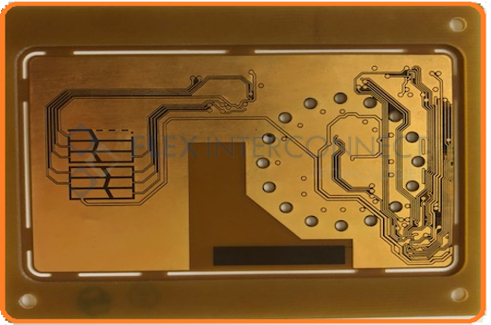
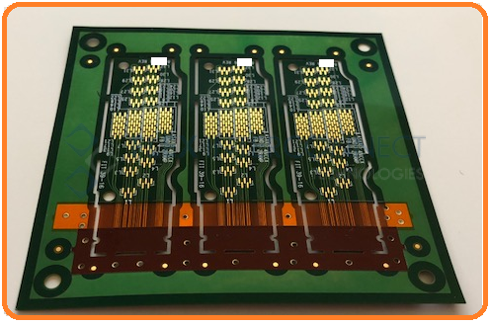
Guide to ordering Stencils:
- Typically 4 mil thick
- Occasionally 3 mil thick or step down stencil may be needed
- Coated stencil needed for micro BGA
- Add fiducials on stencil to align properly
- Mini stencil for offline printing is commonly utilized and sometimes components are loaded by hand
- Stiffeners or FR-4 guides are used to align mini-stencils
Baking Guidelines:
- Polyimide laminates and adhesives absorb up to 3% by weight of moisture
- All flex circuits should be prebaked at 125℃ for 2 to 6 hours
- Moisture uptake for Acrylic adhesives at 80% relative humidity and 23℃:
● 0.65% by weight in 2 hours
● 1% in 10 hours
● 1.2% in 2 days
- Moisture in flex creates very high vapor pressure during re-flow:
● At 220℃ the vapor pressure of water is about 340 psi
● At 230℃ the vapor pressure of water is about 400 psi
● At 260℃ it increases to approximately 700 psi
- Maximum storage time at 50% humidity is 8 hours
Reflow Parameters:
- Ramp rate is slower, approximately 2.5℃ per second
- Peak temperature for pure flex for RoHS assembly is 220℃
- Soak time is kept at minimum – 30 seconds or less
- Rules for rigid-flex are similar to rigid PCB
- Always use thermocouples to profile the reflow oven
Challenges you can expect with assembling Flex:
- Dimensional stability of the flex material – thinner is worse
- Warpage or deformation after one side assembly
- Registration of solder paste
- Pick and Place programming – sometimes have to manually teach each array at a time if proper fiducials are not present
- Handling
- Moisture
- Solid copper shields
- Component Misalignment
- Rework
- Productivity and Cost – NRE and labor costs are higher