We tend to like it when customers come to us as a last resort. It gives us the opportunity to show off our engineering skills. Here’s a design that challenged us in several ways, requiring us to extend our capabilities in order to meet the customer needs.
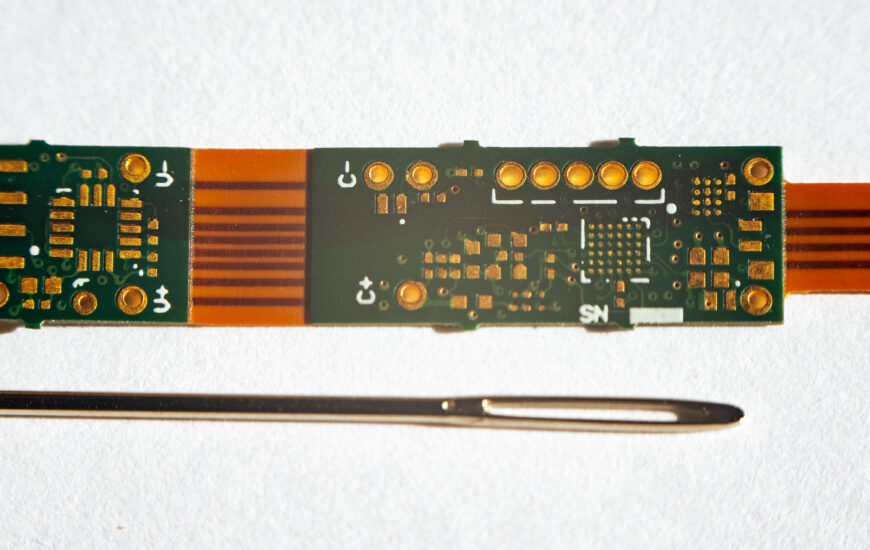
For this project, a medical device manufacturer came to us after several other US-based flex manufacturers passed on their project. Their design was complex, with several features and requirements that would prove challenging to manufacture:
- Small size
- Rigid-flex
- 0.35mm BGA packages on the top and bottom
- 6 layers
- Stacked and staggered microvias on 10mil pads
- Several through holes
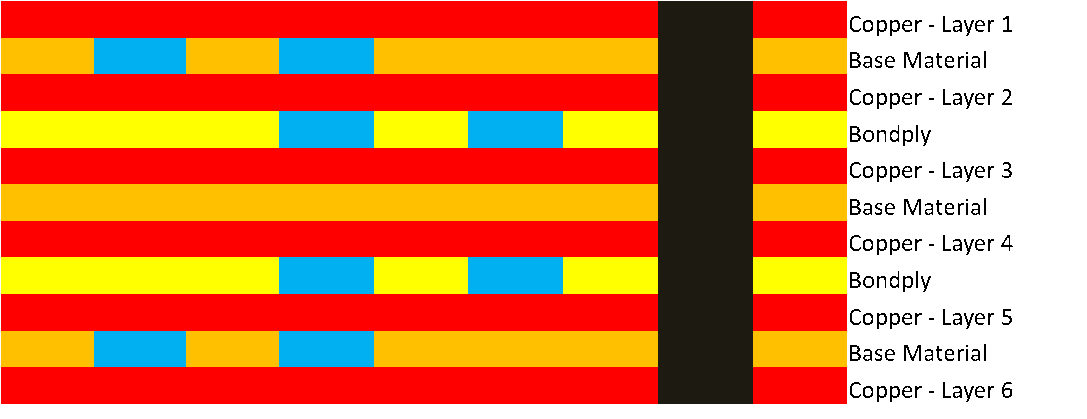
Manufacturing this design required an unconventional approach. Our solution began with all adhesiveless flex laminates, instead of rigid laminates and prepregs.
We also used a copper paste technology from a partner in Japan to form the microvia interconnects. This material ensured we’d meet the customer’s performance requirements, even at such a small scale.
In the end, the component worked, the customer was happy, and we were able to become one of their preferred vendors. What more could we ask for?
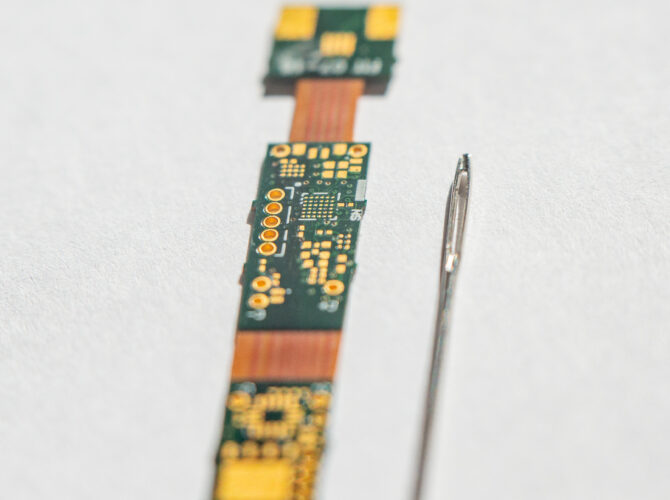
Comments are closed